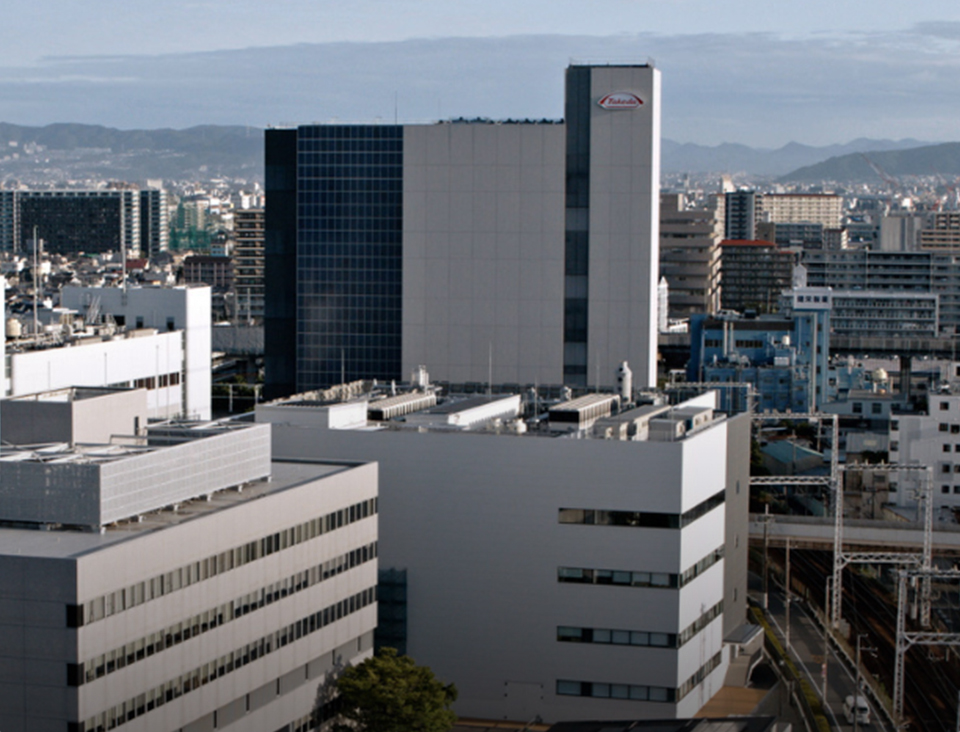
Osaka
Learn About Takeda in Osaka
The Osaka manufacturing facility opened in 1915 to meet the needs of in-house production in Japan and started with the production of Aspirin. We have played a role in Takeda's global production system through the manufacturing of solid formulations, injections, and investigational drugs.
While inheriting the technology and quality cultivated over a history of more than 100 years, we are now an injectable drug site that is taking advanced initiatives to deliver stable, high-quality products to more patients. Today, with approximately 370 employees, we manufacture high-quality sterile preparations and deliver them to patients around the world.
From the Birthplace to the World - Takeda's Roots
Osaka is the birthplace of Takeda, evolving from a small market stall to a global pharma company, and is Takeda’s first manufacturing base in Japan. As an integral part of our Global Manufacturing and Supply Division (GMS), Osaka is responsible for manufacturing injectables as one of the world's key manufacturing sites.
Innovation is at the heart of Osaka, where it is one of the first to work on cutting-edge technologies in each generation, such as automating the supply of raw materials through computer control to product shipment and setting up manufacturing sites in a highly sterile and dust-free environment to deliver high-quality products to countries around the world.
Further Evolution - Anticipating the Next 100 Years
At the Osaka manufacturing facility, there is a technology building that serves as the foundation for Biopharmaceutical Formulation Technology. It has the latest seismic isolation structure and along with the solar power generation system installed on the outer wall, supports a stable product supply system.
In 2016, a microcapsule manufacturing site for injectables was built, in which all processes are performed in a sterile environment. Isolator technology was introduced for delicate and precise work processes to be performed in a sterile environment. A glove port for workers and the latest industrial robot with a multi-axis structure, installed in the isolator, make it possible to maintain the highest level of sterilization in the environment.
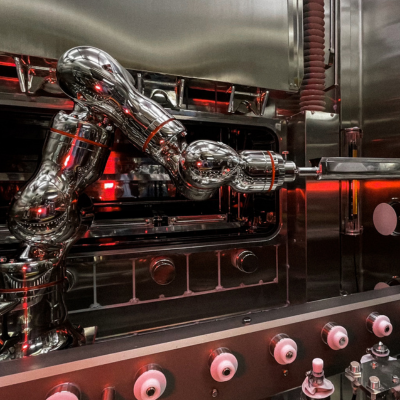
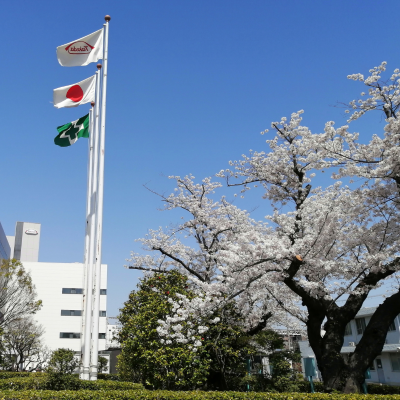
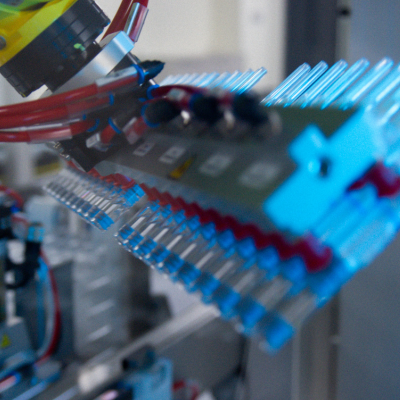
Striving Towards the Future
Strict and Unwavering Quality Control
The quality of pharmaceuticals, which affect human lives, must be manufactured as designed. For this reason, manufacturing control and quality control of drugs are strictly enforced. In addition to being manufactured following GMP (Good Manufacturing Practice: Standards for Manufacturing and Quality Control of Pharmaceuticals) established by Japan, Takeda also manufactures in accordance with the GMP of the countries where it sells its products.
Starting with the acceptance of raw materials and packaging materials, we can finally ship after passing multiple inspections and tests, such as sampling inspections in each manufacturing process, product appearance inspections, physical and chemical tests, microbiological tests, and packaging product tests. Various checks are repeated to ensure that our products can be used with peace of mind.
In 2021, we received regulatory approval for Alofisel, our first stem-cell therapy product for Takeda, Japan, a product that utilizes the latest technology in its manufacturing process. For example, the isolator, which was introduced for the first time in Alofisel's manufacturing network, enables rapid sterilization (ultra-fast decontamination) and maximizes product quality.
We have also established a dedicated logistics system that enables administration within 72 hours. Thanks to the efforts of the team in charge, this Alofisel manufacturing technology was successfully transferred over quickly and efficiently from the Madrid Facility in Spain, where the product was originally produced, even during the pandemic period.
Supported by Technology and People
Osaka also operates a new manufacturing facility for Leuplin, one of Takeda's major oncology products. State-of-the-art equipment, such as isolators (manufacturing equipment that can physically separate sterile products from workers who would cause contamination), automatic inspection machines equipped with deep learning functions, robots and cobots (collaborative robots), and other technology have been introduced.
This has helped to reduce human error, implement electronic data and document management systems, and incorporate dashboards for process monitoring and big data analysis to improve manufacturing efficiency, quality, and compliance. Furthermore, as part of our investment in our people, we are focusing on ensuring high-quality conversations that build relationships of trust and lead to growth and results, reskilling, and fostering a learning culture.
Osaka is the birthplace of Takeda, evolving from a small market stall to a global pharma company, and is Takeda’s first manufacturing base in Japan.
Aiming to Be an Environmentally Friendly Factory
In 2000, we obtained ISO14001 certification, an international standard for environmental management systems. We are strengthening our environmental management system and working on continuous improvements, such as waste reduction (zero emission) activities.
We are striving day and night to create a pollution-free and clean local environment by adopting a thorough system for treating wastewater from the site in the wastewater treatment layer, reducing nitrogen oxides by improving boiler combustion and preventing increases in water and air pollution.
We have also developed and utilized DENSKE, a dashboard that allows anyone to check the status of electricity and water consumption, and we are making progress toward achieving our sustainability goals.
Sharing the Future as a Member of the Local Community
At the Osaka manufacturing facility, we want to be a presence that is always trusted by the local community. As a disaster prevention measure for large-scale disasters, etc., we have registered as an Osaka City Tsunami Evacuation Building. We regularly plant greenery in vacant lots on the site and clean up the surrounding area.
Furthermore, we aim to create a site that can coexist in harmony with the future by asking residents to become "environmental monitors" and conducting surveys on noise and odors on-site.
Aiming to Become a “Factory of the Future”
The Osaka manufacturing facility is taking the lead in the digital transformation (DX) of our manufacturing, aiming to become a “Connected & Predictive Site” by utilizing data to predict and avoid possible deviations and risks in the manufacturing process, supply, quality, compliance, and efficiency.
Osaka Employee Experience
Some Highlights of Our Benefits:
- Allowances: Commutation, Housing, Overtime Work, etc.
- Salary Increase: Annually
- Bonus Payment: Twice a year
- Working Hours: Headquarters (Osaka/ Tokyo) 9:00-17:30, Production Sites (Osaka/Yamaguchi) 8:00-16:45, (Narita) 8:30-17:15, Research Site (Kanagawa) 9:00-17:45
- Holidays: Saturdays, Sundays, National Holidays, May Day, Year-End Holidays, etc. (approx. 123 days in a year)
- Paid Leaves: Annual Paid Leave, Special Paid Leave, Sick Leave, Family Support Leave, Maternity Leave, Childcare Leave, and Family Nursing Lea
- Flexible Work Styles: Flextime, Telework
- Life Planning programs: Retirement, Employee Stock Ownership Program, etc.
- Healthcare and insurance
-
Our Hikari Facility Learn more about our Hikari manufacturing facility in Japan
-
Our Narita Facility Learn more about our Narita manufacturing facility in Japan
Manufacturing and Supply: Osaka
Our Location
-
2-17-85 Jusanhonmachi, Yodogawa-ku, Osaka 532-8686
Jobs for you
- HR Partner or HR Site Leader 光工場/大阪工場/成田工場 Hikari, Japan, Chiba, Japan, Jūsō-honmachi, Japan Category: Human Resources
- Operator, Sterile Production, Osaka Plant / 大阪工場 注射剤製造担当者(契約社員) Jūsō-honmachi, Japan Category: Manufacturing/Production
- Procurement Business Partner, Global Finance, Japan/ ジャパン グローバルファイナンス 購買ビジネスパートナ(課長代理) Jūsō-honmachi, Japan, Hikari, Japan Category: Finance
- Manager, People Resource Hub & Employee Lifecycle Management, Takeda Business Solutions Osaka, Japan, Tokyo, Japan Category: Human Resources