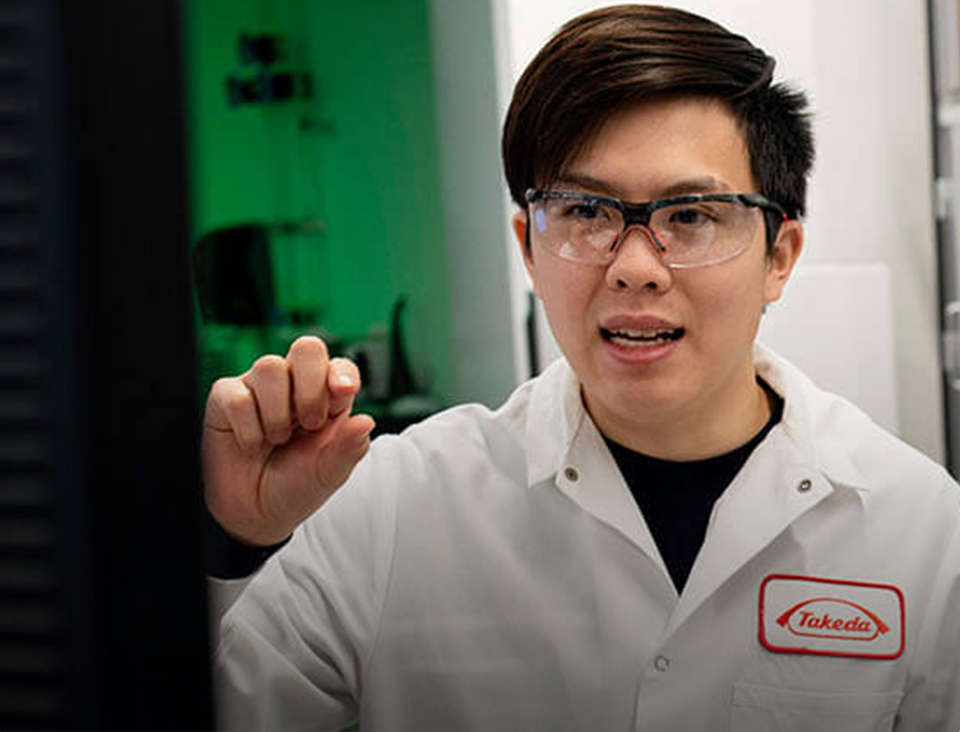
Your next challenge: Driving rapid change with your ideas
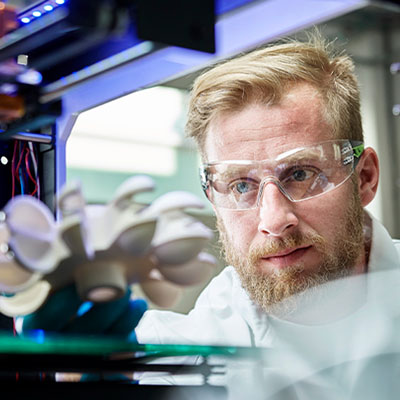
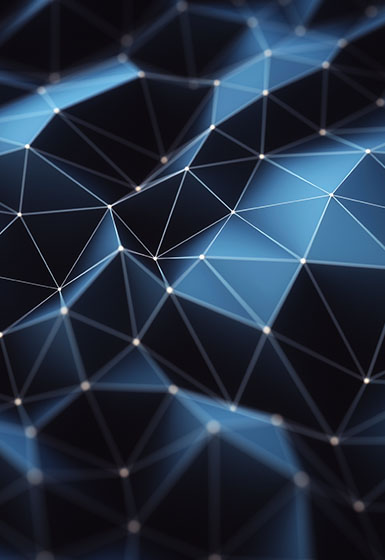
We’re empowering employees to transform our operations.
Picture this: You have a great idea on how to fix a common challenge. It could be as simple as making a tool easier to use — or as complex as redefining a manufacturing process. But there’s a catch. You need to turn it around quickly and avoid downtime costs. With resources like 3D printing, employees can transform how Takeda manufacturing sites work.
Here’s how it works. Employees propose an idea to an engineer who can rapidly test it, then make any necessary changes or improvements.
"…we can bring it to life in a couple of iterations," says Dominic Duda, Global Engineering Technology Solution Lead. "It’s 'This is what I need, can we connect these two parts?' and the engineer says, 'Yes, give me two hours.'"
The process provides Takeda employees a safe environment to spot and fix problems before going into full development. With tools like 3D printing, employees can now bring forward more ideas that can be executed in shorter times inexpensively. Lead robotics engineer Luiz Esteves, said it best. "That’s the beauty of 3D printing – we can be more creative."
While 3D printing has proven to be valuable for producing one-offs such as prototypes and rare replacements, it also allows for customization and increased efficiency.
At our Hikari plant, vials in the conveyer belt would often tip over, blocking the supply line and increasing production time. Our local engineering team and shopfloor operators collaborated and identified which parts of the machine affected the vials and tested small changes to improve the flow.
Another advantage of resources like 3D printing is significantly reducing employee training time. Where past training for employees within our facilities could take up to a month, now trainees can make use of inexpensive mockups. The result? Training time and costs have been reduced and new team members are able to start contributing faster than they ever have been.
This fix led to a 68% reduction in the number of fallen bottles and reduced bottle handling time by 20 hours a year.
The enormous appeal of reducing assembly inefficiencies inspired Giuseppe Bonfiglio, a Line Technician at Takeda's Lessines manufacturing site. He gave a sketch to Takeda's engineering team and, using 3D printing, they created and tested five designs in plastic before deciding on the best solution to reproduce in sterile stainless steel.
Luiz is now working to get the word out across our manufacturing sites that this technology exists, so our employees will feel motivated to bring forward more ideas. As a result, our organization will continue to evolve.
If you’re ready to build a meaningful career where you will be empowered to develop life-changing innovative solutions, why not consider Takeda?
Jobs for you
- Associate Director Quality Assurance Los Angeles, California Category: Quality
- Manufacturing Technician II Los Angeles, California Category: Manufacturing/Production
- Manufacturing Technician II Los Angeles, California Category: Manufacturing/Production
- B5 Pre-Viral Manufacturing Technician II Los Angeles, California Category: Manufacturing/Production